In the manufacturing and converting industries, slitter-rewinders play a vital role in the production of a wide range of materials, especially in the paper, film and foil industries. Understanding how a slitter-rewinder works is critical for those working in these industries, as it can have a significant impact on the efficiency and quality of the final product. This article will take an in-depth look at the mechanical principles, components and operating procedures of a slitter rewinder.
A slitter is a machine designed to cut large rolls of material into narrow rolls or sheets. This process is known as slitting and is commonly used for materials such as paper, plastic film, tape and non-woven fabrics. The machine's rewinding job is to roll the slit material back onto a mandrel and rewind it into smaller, more manageable rolls for further processing or distribution.
Key Components of Slitting and Rewinding Machines
To understand how a slitter and rewinder works, it is important to familiarise yourself with its key components:
1. Unwinding station: This is where large master rolls of material are installed. The unwind station is equipped with a tension control system to ensure that the material is fed into the machine at a consistent speed and tension.
2. slitting blades: these are very sharp blades that cut the material into narrower strips. The number and configuration of blades can vary depending on the desired width of the finished product. Slitting blades can be rotary, shear or razor blades, each offering different advantages depending on the material being processed.
3. Slitting Table: This is the surface that guides the material through the longitudinal cutting blade. The slitting table is designed to keep the material aligned to ensure an accurate cut.
4. Winding Station: After the material is slit, it is wound onto the core at the winding station. The winding station is equipped with a tension control system to ensure that the web is wound evenly and without defects.
5.Control systems: Modern slitters and rewinders are equipped with advanced control systems that allow the operator to monitor and adjust various parameters such as speed, tension and blade position. This automation increases efficiency and reduces the possibility of errors.
If you have any requirements about this type products, please check out company’s this product, named LQ-L PLC High Speed Slitting Machine manufacturers
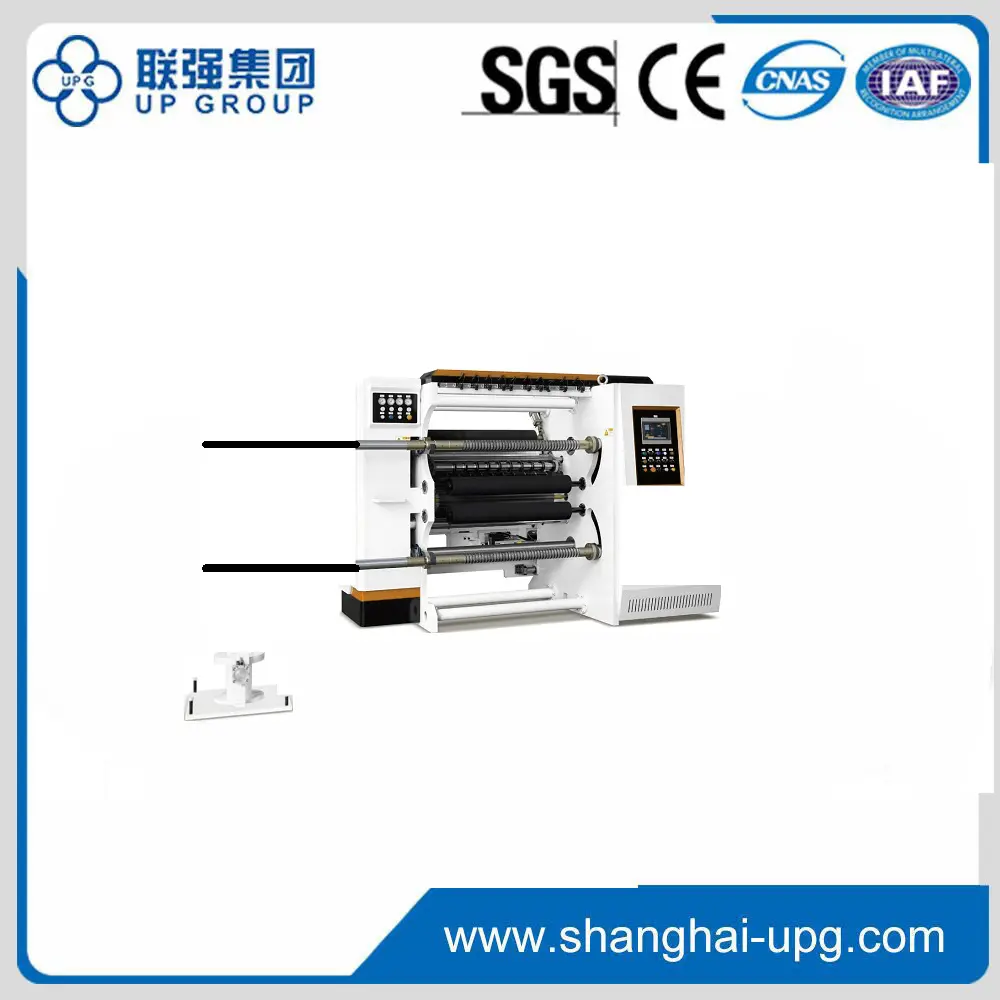
The Servo Drive High Speed Slitting Machine applies to slit cellophane, The Servo Drive High Speed Slitting Machine applies to slit PET, The Servo Drive High Speed Slitting Machine applies to slit OPP,The Servo Drive High Speed Slitting Machine applies to slit CPP, PE, PS, PVC and computer security labels, electronic computers, optical materials, film roll, foil roll, all kinds of paper rolls.
Slitting and rewinding process
The operation of a slitter and rewinder can be divided into several key steps:
1. Expanding the material
A large master roll is first installed at the unwind station. The operator sets the machine to the desired speed and tension to ensure that the material feeds smoothly into the slitting area. The unwind station may also include a braking system to maintain stable tension while unwinding.
2. Cutting the material
When material is fed into the slitting area, it passes through the slitting blades. The blades cut the material to the required width, which varies from a few millimetres to several centimetres, depending on the application. Accuracy in the slitting process is critical, as any errors can lead to waste and quality issues.
3. Guide gap material
After the material has been cut, it moves along the cutting table. The cutting table ensures that the strip remains aligned and prevents any misalignment that could lead to defects. At this stage, the operator may need to adjust alignment and tension to maintain quality.
4. Material Rewinding and Slitting
Once the material is cut, it is sent to the rewinding station. Here, the cut tape is wound onto a paper core to form smaller rolls. The tension control system at the rewinding station ensures that the rolls are wound evenly and tightly, preventing any loose or uneven winding that could affect the usability of the final product.
5. Quality control and finishing
Once the rewinding process is complete, the finished rolls are checked for quality. This may include checking for defects, measuring the width and diameter of the rolls, and ensuring that the material meets the required standards. Any rolls that do not meet quality standards may be reprocessed or discarded.
Benefits of using slitters and rewinders
Using a slitter rewinder offers several benefits to manufacturers:
- Efficient: Slitting and rewinding machines can process large quantities of material quickly, resulting in shorter production times and higher yields.
- Precision: With advanced control systems and sharp slitting blades, these machines make precise cuts, minimising waste and ensuring a high quality product.
- Versatile: Slitting and rewinding machines can handle a wide range of materials and are suitable for a variety of applications in different industries.
- Cost-effective: By optimising the slitting and rewinding process, manufacturers can reduce material costs and improve overall profitability.
In short, slitter rewinders are an essential piece of equipment for the converting industry, enabling manufacturers to efficiently cut and rewind materials into smaller, usable rolls. Understanding how a slitter rewinder works, from the unwinding of the master roll to the final quality control checks, is critical for anyone involved in the production process. By utilising the capabilities of a slitter rewinder, manufacturers can improve operational efficiencies, reduce waste and deliver a high quality product to their customers.
Post time: Dec-16-2024