Blow moulding is a widely used manufacturing process for making hollow plastic parts. It is particularly popular in the production of containers, bottles and various other products. At the heart of the blow moulding process is the blow moulding machine, which plays a vital role in moulding the plastic material into the desired product. In this article, we will look at the four stages of blow moulding and how a blow moulding machine facilitates each stage.
Before delving into each stage, it is necessary to understand what blow moulding is. Blow moulding is a manufacturing process that involves blowing a heated plastic tube (called a parison,) into a mould to form a hollow object. The process is efficient and affordable, making it a popular choice for producing large quantities of plastic products.
The four stages of blow moulding:
Blow moulding can be divided into four distinct stages: extrusion, forming, cooling and ejection. Each stage is critical to the overall success of the blow moulding process, and blow moulding machines facilitate each stage.
1. Extrusion
The first stage of blow moulding is extrusion, where plastic pellets are fed into a blow moulding machine. The blow moulding machine heats the plastic pellets until they melt, forming a continuous tube of molten plastic called a parison. The extrusion process is critical because it determines the thickness and uniformity of the parison, which directly affects the quality of the final product.
At this stage, the blow moulding machine uses a screw or plunger to push the molten plastic into the mould to form the parison. Temperature and pressure must be carefully controlled to ensure that the plastic is completely melted and can be easily moulded in subsequent stages.
2. Forming
Once the parison is formed, the moulding stage is entered. In this stage, the parison is clamped into the mould to shape the final product. The blow moulding machine then introduces air into the parison, causing it to expand until it completely fills the mould. This process is known as blow moulding.
The design of the mould is critical as it determines the final size and surface finish of the product. At this stage, the blow moulding machine must precisely control the air pressure and temperature to ensure that the parison expands uniformly and adheres to the walls of the mould.
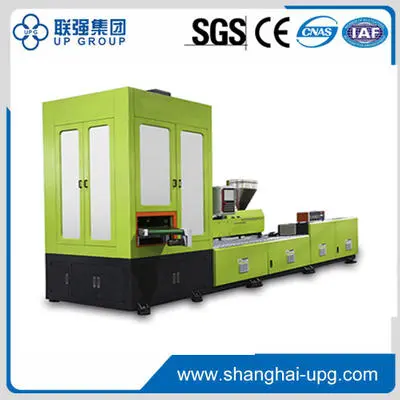
1. The AS series model uses three-station structure and is suitable for producing plastic containers such as PET, PETG, etc. It is mainly used in packaging containers for cosmetics, pharmaceutical, etc.
2. Injection-stretch-blow molding technology consists of machines, molds, molding processes, etc. Liuzhou Jingye Machinery Co., Ltd. has been researching and developing this technology for more than ten years.
3. Our Injection-Stretch-Blow Molding Machine is three-station: injection preform, strentch & blow, and ejection.
4. This single stage process can save you much energy becuase you do not have to reheat the preforms.
5. And can ensure you better bottle appearance, by avoiding preforms scratching against each other.
3. Cooling
After the parison has been inflated and moulded, it enters the cooling phase. This stage is essential for curing the plastic and ensuring that the final product retains its shape. Blow moulding machines usually use cooling channels or air to reduce the temperature of the moulded part.
The cooling time varies depending on the type of plastic used and the thickness of the product. Proper cooling is critical because it affects the mechanical properties and overall quality of the final product. If the cooling process is not properly controlled, it may result in warpage or other defects in the finished product.
4. Ejection
The final stage of blow moulding is ejection. Once the product has cooled and solidified, the blow moulding machine opens the mould to release the finished product. This stage must be done carefully to avoid damaging the product. The machine may use a robotic arm or ejector pin to assist in removing the part from the mould.
After ejection, the product may have to go through other processing steps, such as trimming or inspection, before it can be packaged and shipped. The efficiency of the ejection stage can have a significant impact on the overall production cycle and is therefore a critical part of the blow moulding process.
Blow moulding is an efficient and versatile manufacturing process that relies on the precise operation of the blow moulding machine. By understanding the four stages of blow moulding (extrusion, forming, cooling and ejection), it is possible to gain an insight into the production of hollow plastic products. Each stage plays a vital role in ensuring the quality and consistency of the final product.
As the demand for high-quality plastic products continues to grow across a wide range of industries, advances in blow moulding technology and machinery are likely to increase the efficiency and capability of the blow moulding process. Whether you are a manufacturer, engineer, or simply interested in the world of plastics production, understanding these stages will deepen your understanding of the complexity and innovation behind blow moulding machines.
Post time: Dec-09-2024