Injection molding is a widely used manufacturing process that produces parts by injecting molten material into a mold. This technique is particularly popular in the production of plastic parts, but can also be used for metals and other materials. The injection molding machine is the heart of the process and plays a crucial role in determining the quality, efficiency and cost-effectiveness of the final product. This article will explore the three basic types of injection molding machines and their unique functions.
Hydraulic Injection Molding Machines
Hydraulic injection molding machines are the most traditional and commonly used type of injection molding machine in the industry, and they use a hydraulic system to generate the force needed to inject molten material into the mold. The key components of a hydraulic machine include hydraulic pumps, hydraulic cylinders and hydraulic valves, which together control the flow and pressure of the hydraulic fluid.
Advantages:
High clamping force: Hydraulics and can generate large clamping forces, making them suitable for large and complex molds.
Versatility: Can handle a wide range of materials, including all types of materials and composites.
Cost-effective for mass production: for mass production, hydraulic presses are more economical due to their durability and ability to maintain consistent quality.
Disadvantages:
Energy consumption: Hydraulic systems tend to consume more energy than other types of machines, resulting in higher operating costs.
Maintenance requirements: Hydraulic components require regular maintenance to ensure optimum performance, which can increase downtime.
You can take a look at this one of our LQS Series Servo Motor Injection Molding Machine Supplier,
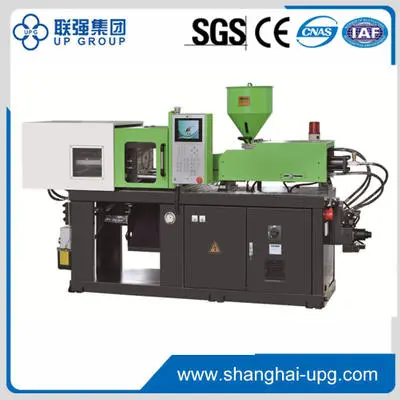
Features:
1. Double cylinder balanced injection system;
2. Multi-stage pressure &speed injection;
3. Back pressure adjustment device;
4. Low-pressure mould protection;
5. Single hydraulic core pulling and inserting;
6. Multiple hydraulic ejector knock-out;
7. Mechanical, electrical safety device;
8. Auto lubrication system;
9. Hydraulic pressure full proportional control;
10. Computer control system;
11. Molding data memory system;
12. Automatic mould adjust function;
13. Energy-saving with servo motor;
Electric injection molding machine
Electric injection molding machines have become increasingly popular this year due to their high energy efficiency and precision. These machines use electric motors to drive the injection molding process, eliminating the need for hydraulics. Key components include servo motors, ball screws and linear guides, which work together to provide precise control of the injection molding process.
Advantages:
-High energy efficiency: motors use electricity only when needed, resulting in lower energy consumption and thus lower operating costs.
-Precision and repeatability: the use of servomotors allows precise control of injection speeds and pressures, thus ensuring consistent part quality.
-Reduced noise levels: motors operate at lower noise levels than hydraulic machines, making them suitable for environments where noise reduction is a priority.
Disadvantages:
-Higher initial cost: the higher upfront cost of electric injection molding machines compared to hydraulic machines can be a barrier for some manufacturers.
-Limited clamping capacity: While electric motors can handle a variety of applications, they may not be able to generate the same clamping force as hydraulic machines, making them less suitable for very large molds.
Hybrid Injection Molding Machines
Hybrid injection molding machines combine the advantages of hydraulic machines and electric motors. They utilize a hydraulic system for clamping and an electric drive for injection, achieving a balance between power and efficiency. Such machines are designed to optimize performance while minimizing energy consumption.
The advantages:
-Best of both worlds: Hybrid machines offer the high clamping capacity of a hydraulic system with the energy consumption and precision of an electric system.
-Flexibility: They can be used in a wide range of applications and are suitable for manufacturers with different production needs.
-Shorter cycle times: the combination of hydraulic and electric components reduces cycle times and increases overall productivity.
Disadvantages:
-Complexity: the integration of hydraulic and electrical systems can make hybrid machines more complex and may lead to higher maintenance requirements.
-Cost considerations: While hybrid machines offer many advantages, they can also be more expensive, which may not be applicable to all manufacturers.
Injection molding machines are an essential tool in manufacturing. Understanding the three basic types (hydraulic, electric and hybrid) helps manufacturers make an informed decision based on their specific needs. Each type has its own advantages and disadvantages, and the choice ultimately depends on factors such as production volume, material requirements and budgetary constraints.
Post time: Nov-11-2024