Thermoforming, as it is known, is a common manufacturing process used to shape plastic materials into a variety of products. It involves heating a thermoplastic sheet until it becomes pliable, then moulding it into a specific shape using a mould and finally cooling it to solidify. The process is widely used in industries such as packaging, automotive, medical and consumer goods. It is common for certain companies to invest in automated thermoforming machines in order to perform thermoforming efficiently, streamlining the production process and ensuring consistent quality. Next, let's take a look at the two most common types of thermoforming and how automated thermoformers can improve production.
Two of the most common types of thermoforming are vacuum forming and pressure forming. Vacuum forming is a simplified version of thermoforming, in which thermoplastic sheets are heated and then stretched over a mould using vacuum pressure. This method is usually used to produce large, shallow products such as packaging and panels. Pressure moulding, on the other hand, uses vacuum pressure and the additional pressure of a plug to help form the plastic sheet over the mould, producing products with more intricate details and sharper contours, such as automotive parts, medical devices and electronic housings.
The production process can be significantly improved with the use of automatic thermoforming machines, which are equipped with automatic feeding, heating, moulding and trimming of the cash, reducing manual intervention and increasing overall productivity. Automatic thermoforming machines also provide precise control over the heating and cooling process, ensuring consistent product quality and reducing wasted material. This automated production not only speeds up production but also minimises errors, resulting in cost savings and improved product quality.
Our company produces automatic thermoforming machines, such as this one
LQ-TM-51/62 Full Automatic Thermoforming Machine manufacturer
Servo driven platen for smooth and energy efficient movement
Memory storage system
Optional working modes
Intelligent diagnostic analysis
Quick mould air baffle change
In-mould cutting ensuring consistent and accurate trim
Low energy consumption, high utilization
Robot with 180 degree rotation and dislocation palletizing
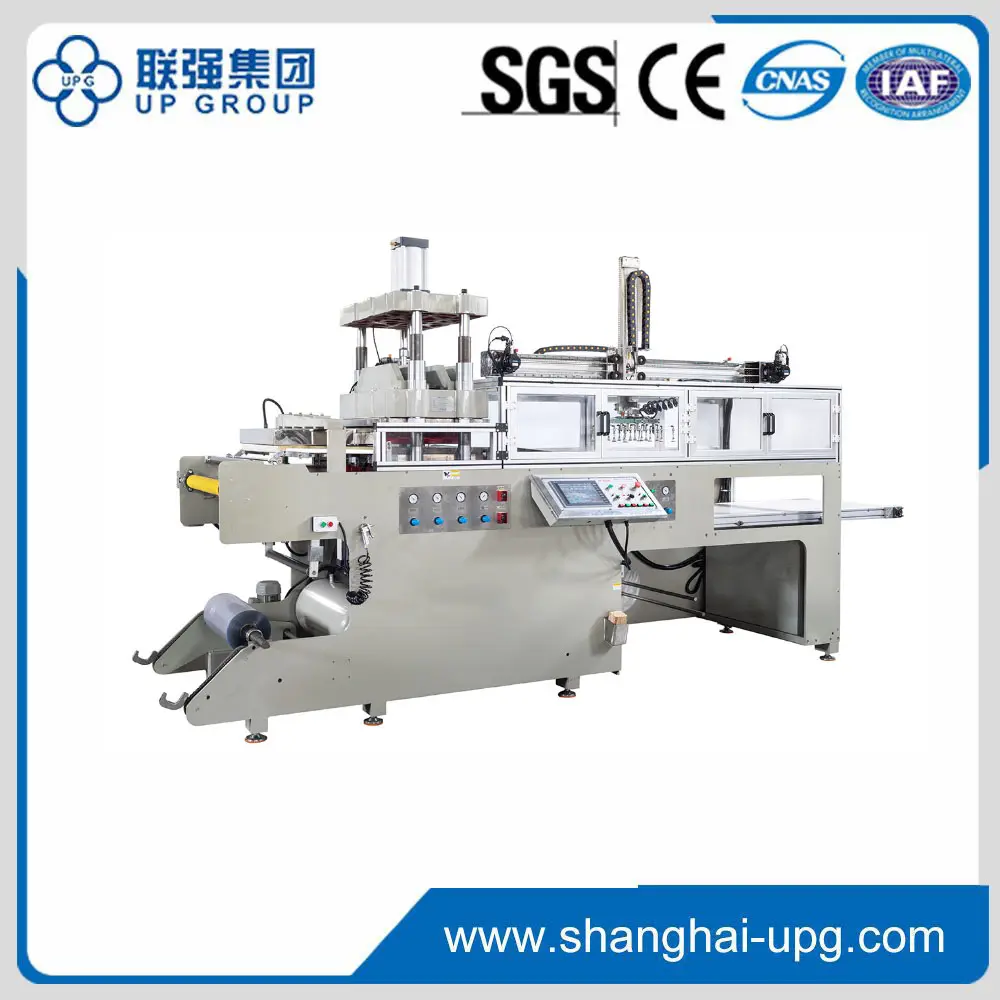
Automatic thermoforming machines, efficiency and versatility are also compelling, saving time and labour through automation, and can produce a wide range of products of consistent quality, in addition, automatic thermoforming machines can reduce material wastage and increase production capacity, resulting in improved cost-effectiveness, which should be a big draw for manufacturers looking to upgrade their thermoforming capabilities. At the same time, automatic thermoforming machines can handle different types of plastics, whether it be PET, PVC, ABS or polycarbonate can be adapted. This adaptability opens up possibilities for companies to expand their product range and enter new markets.
All in all, the two most common types of thermoforming are vacuum and pressure moulding, which play a vital role in manufacturing and are adaptable to a wide range of products. When combined with the capabilities of automated thermoforming, the production process becomes more efficient, precise and economical. Meanwhile, if you have any needs about automatic thermoforming machine, please contact our company in time, for many years we export to all over the world, which greatly improves the production efficiency and product quality of the customer side.
Post time: Jul-01-2024