PET (polyethylene terephthalate) bottles are widely used for packaging beverages, edible oils, pharmaceuticals and other liquid products. The process of making these bottles involves a specialized machine called a PET blow molding machine. In this article, we will take an in-depth look at the PET bottle blowing process and the role of the PET bottle blowing machine in this important manufacturing process.
The process of blowing PET bottles starts with the raw material, which is PET resin. The resin is first melted and then molded into a preform using an injection molding machine. The preform is a tubular structure with a neck and threads that resembles the shape of the final bottle. Once the preforms are produced, they are transferred to the PET blow molding machine for the next stage of processing.
PET bottle blowing machines play a vital role in transforming preforms into final bottles. The machine uses a process called stretch blow molding, which involves heating the preform and then stretching and blowing it into the desired bottle shape. Let’s take a closer look at the key steps involved in blowing PET bottles using a PET bottle blowing machine:
Preform heating: The preform is loaded into the heating part of the machine, where it undergoes a process called preform conditioning. During this stage, the preform is heated to a specific temperature that makes it malleable and suitable for subsequent stretching and blow molding processes. The heating process is carefully controlled to ensure uniform heating and avoid deformation of the final bottle.
Stretching: After the preform reaches the optimal temperature, it is transferred to the stretching station of the PET bottle blowing machine. Here, the preform is stretched axially and radially using stretch rods and stretch blow pins. This stretching helps orient the molecules in the PET material, which increases the strength and clarity of the final bottle.
Bottle blowing: After the stretching process is completed, the heated and stretched bottle preform is moved to the bottle blowing station. During this stage, high-pressure air is injected into the preform, causing it to expand and form the shape of the bottle mold. The mold itself is carefully designed to give the bottle the desired shape, size and features, such as neck and thread details.
Cooling and ejection: After the blow molding process is completed, the newly formed PET bottle will be cooled within the mold to ensure that it maintains its shape and structural integrity. After sufficient cooling, the mold is opened and the finished bottles are ejected from the machine, ready for further processing and packaging.
Meantime, please visit our company’s this product, LQBK-55&65&80 Blow Molding Machine Wholesale
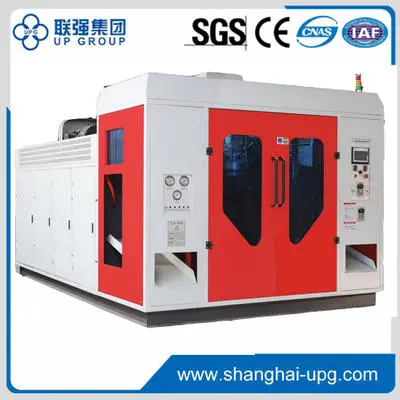
Plastic system: high efficiency and plastic mixing screw,ensure that the plastic is full, uniform.
Hydraulic system: Doubld proportion control, put the frame adopts linear guide rail and mechanical type decompression, run more smoothly, within imported famous brand hydraulic yuan. Device stable speed, low noise, durable.
Extrusion system: frequency variable+toothed surface reducer, stable speed, low noise, durable.
Control system: This machine adopt PLC man- machine interface (Chinese or English)control,touch operation screen operation,can process set,change,search, monitoring, fault diagnosis and other functions can be achieved on the touch screen. Convenient operation.
Die opening and closing system: arm of the girders, third point, central lock mould mechanism, clamping force equilibrium, no deformation, high precision, less resistance, speed and Characteristic.
The entire process of blowing PET bottles using a PET bottle blowing machine is highly automated and efficient, and can achieve high-speed production and stable quality. Modern PET blow molding machines are equipped with advanced features such as infrared heating systems, servo-driven stretch rods and precise control systems to optimize the production process and minimize energy consumption.
In addition to standard single-stage PET blow molding machines, there are also two-stage PET blow molding machines, which contain an intermediate step for creating the preform using an injection molding machine. This two-stage process provides greater production flexibility and allows preforms to be stored for future use, reducing the need for continuous operation of the PET blow molding machine.
The versatility of PET bottle blowing machines enables the production of bottles of various sizes, shapes and designs to meet the diverse packaging needs of various industries. From small single-serve bottles to large containers, PET blow molding machines can be configured to meet different production requirements, making them an integral part of the packaging industry.
In short, the process of blowing PET bottles using a PET blow molding machine is a complex and precise manufacturing process, including heating, stretching and blowing the preform to produce high-quality PET bottles. With advancements in technology and automation, PET bottle blowing machines continue to play a key role in meeting the growing demand for PET bottles across different industries. As the packaging industry develops, PET bottle blowing machines will undoubtedly continue to innovate and adapt to the changing needs of the market, ensuring efficient production of reliable and sustainable packaging solutions.
Post time: Sep-07-2024