In today's fast-paced world, plastic containers have become an integral part of our daily lives. From food storage to industrial applications, these versatile products are manufactured using advanced plastic container machinery. Understanding the manufacturing process of plastic containers not only provides an understanding of the technology involved, but also highlights the importance of sustainability in the industry.
Plastic container machinery includes a range of equipment used to produce plastic containers in a variety of shapes, sizes and materials. These include injection molding machines, blow molding machines, extruders and thermoformers. Each type of machinery plays a vital role in the production process, ensuring efficiency, precision and quality of the final product.
Below is the types of Plastic Container Machinery
Injection Molding Machines: These machines are used to create complex shapes and designs. The production process involves melting plastic pellets and injecting the molten plastic into the mold. After cooling, the mold is opened and the solidified container is ejected. This method is ideal for producing containers with intricate details and high precision.
Extruder: Extrusion is a continuous process in which plastic is melted and forced through a die to form a specific shape. This method is typically used to produce flat plates or tubes, which are then cut and molded into containers. Extruders are particularly well suited for producing large quantities of uniform products.
Thermoformer: In this process, a plastic sheet is heated until it is pliable and then molded over a die. Upon cooling, the molded plastic will retain its shape. Thermoforming is commonly used to make shallow containers such as trays and clamshell packages
Here we would like to introduce to you one of our company produced, LQ TM-3021 Plastic Positive And Negative Thermoforming Machine
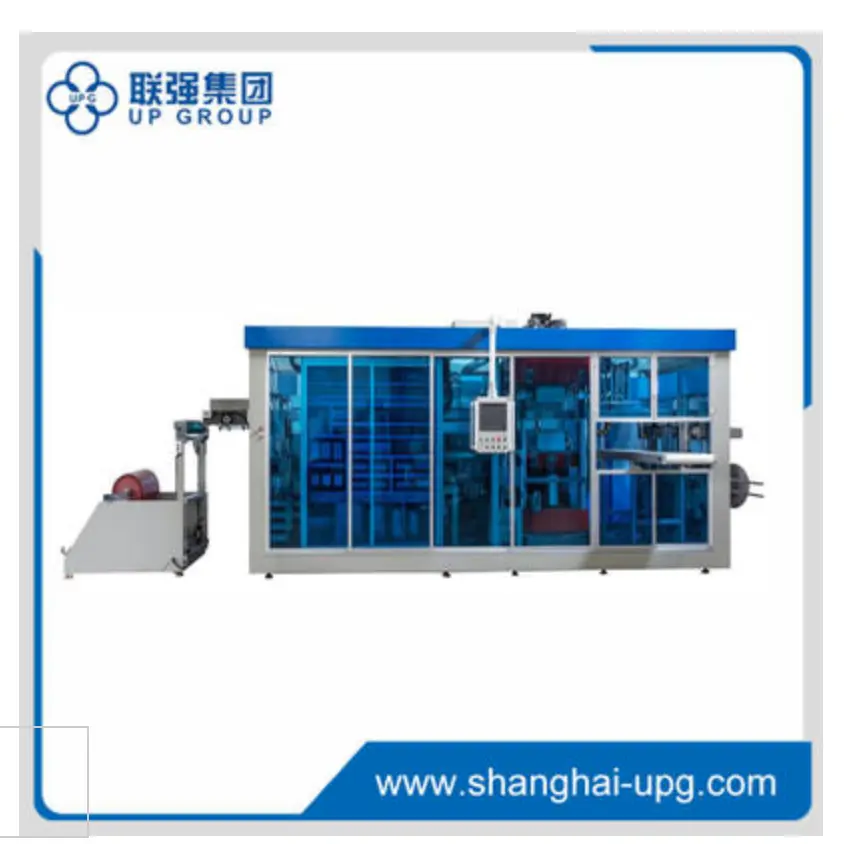
Main features are
● Suitable for PP, APET, PVC, PLA, BOPS, PS plastic sheet.
● Feeding, forming, cutting, stacking are driven by servo motor.
● Feeding, forming, in-mould cutting and stacking processing are complete production automatically.
● Mould with rapid change device, easy maintenance.
● Forming with 7bar air pressure and vacuum.
● Double selectable stacking systems.
Plastic Container Manufacturing Process
The production of plastic containers involves several key steps, each assisted by specialized machinery and equipment. This process is described in detail below:
1. Material Selection
The first step in manufacturing plastic containers is to select the right type of plastic. Common materials include polyethylene (PE), polypropylene (PP) and polyvinyl chloride (PVC). The choice of material depends on the intended use of the container, the required durability and regulatory compliance, especially for food grade applications.
2. Material Preparation
Once the material has been selected, it is prepared for processing. This includes drying the plastic pellets to remove moisture, which can affect the quality of the final product, and then feeding the pellets into the machine for melting and molding.
3. Molding Process
Depending on the type of machinery used, the molding process can vary:
Injection molding: Dry pellets are heated until they melt and then injected into the mold. The mold is cooled to allow the plastic to solidify and then ejected.
Blow Molding: A parison is made and heated. The mold is then inflated to form the shape of the container. After cooling, the mold is opened and the container is removed.
Extrusion: The plastic is melted and forced through the mold to form a continuous shape, which is then cut to the desired length of the container.
Thermoforming: The plastic sheet is heated and molded on a template. After cooling, the molded container is trimmed and separated from the plastic sheet.
4.Quality Control
Quality control is a critical step in the production process. Each container is inspected for defects such as warping, uneven thickness or contamination. State-of-the-art machinery often includes automatic inspection systems that detect defects in real time, ensuring that only high quality products reach the market.
5. Printing and labeling
Once the container has been molded and inspected, the printing and labeling process can take place. This includes the addition of brand logos, product information and barcodes. Specialized printing machinery ensures that graphics are accurately attached to the plastic surface.
6.Packaging and Distribution
7. The final step in the production process is to package the containers for distribution, which involves grouping the containers (usually in bulk) and preparing them for shipment. Efficient packaging machinery helps to streamline this process, ensuring that the product is ready for delivery to the retailer or end user.
Sustainability in plastic container manufacturing
As the demand for plastic containers continues to grow, so does the need for sustainability in their manufacturing. Many companies are investing in eco-friendly materials such as biodegradable plastics and recycled materials. Additionally, advances in plastic container machinery are enabling manufacturers to reduce waste and energy consumption during the manufacturing process.
In short, the process of manufacturing plastic containers is a complex interaction of technology, material science and quality control, all of which cannot be achieved without specialized plastic container machinery. As the industry evolves, embracing sustainability and innovation while minimizing the impact on the environment while meeting consumer needs will be critical, and understanding this process not only highlights the complexity of modern manufacturing, but also underscores the importance of taking a responsible approach to plastic container production.
Post time: Oct-21-2024