Plastic containers are ubiquitous in all walks of life, from food packaging to storage solutions, the demand for plastic containers continues to rise, and accordingly can contribute to the development of machinery designed to efficiently produce containers. In the next section, we'll look at the different types of plastic container machinery and the processes involved in manufacturing plastic containers.
Plastic container machinery refers to specialized equipment used to produce plastic containers. This machinery covers a range of technologies and processes, including injection molding, blow molding, and thermoforming, and each method has its own unique advantages for different types of plastic containers.
1. Injection Molding Machines
One of the most common methods of manufacturing plastic containers, injection molding involves melting plastic pellets and injecting the molten plastic into a mold. Once the plastic has cooled and solidified, the mold is opened and the finished container is injected.
Key features of an injection molding machine:
-Precision: injection molding machines are known for their ability to produce highly detailed, complex shapes with tight tolerances.
-Speed: Injection molding has a relatively short cycle time, allowing for mass production.
-Material Versatility: Injection molding can use a wide range of thermoplastics, making it suitable for a variety of applications.
Injection molding is ideal for the production of containers such as jars, bottles and other rigid packaging solutions.
2. Blow Molding Machines
Blow molding is another common method for producing plastic containers, especially hollow containers such as bottles. The process begins with the creation of a tubular plastic mold blank. The parison is then placed into a mold into which air is blown to expand the plastic and form the shape of the mold.
Key features of blow molding machines:
-High efficiency: blow molding is very effective for producing large quantities of hollow containers.
-Lightweight containers: This method allows for the production of lightweight containers, which reduces transportation costs and environmental impact.
-Variety of shapes: blow molding can produce containers of various shapes and sizes, from small bottles to large industrial containers.
Blow molding is commonly used to manufacture beverage bottles, detergent containers and other similar products.
3. Thermoforming Machine
Thermoforming is the process of heating a sheet of plastic until it is pliable and then molding it into a specific shape using a mold. The plastic cools down and maintains the shape of the mold, resulting in a finished container.
Key features of thermoforming machines:
-Cost-effective: thermoforming is usually more cost-effective than injection molding or blow molding when producing shallow containers and trays.
-Rapid prototyping: This method allows for quick design changes, making it suitable for prototyping and small batch production.
-Material efficiency: Thermoforming allows for efficient use of waste materials and reduces waste.
Thermoforming is commonly used to produce food containers, clamshell packaging and disposable cups.
You can take a look at this one produced by our company, LQ250-300PE Film Double-Stage Pelletizing Line
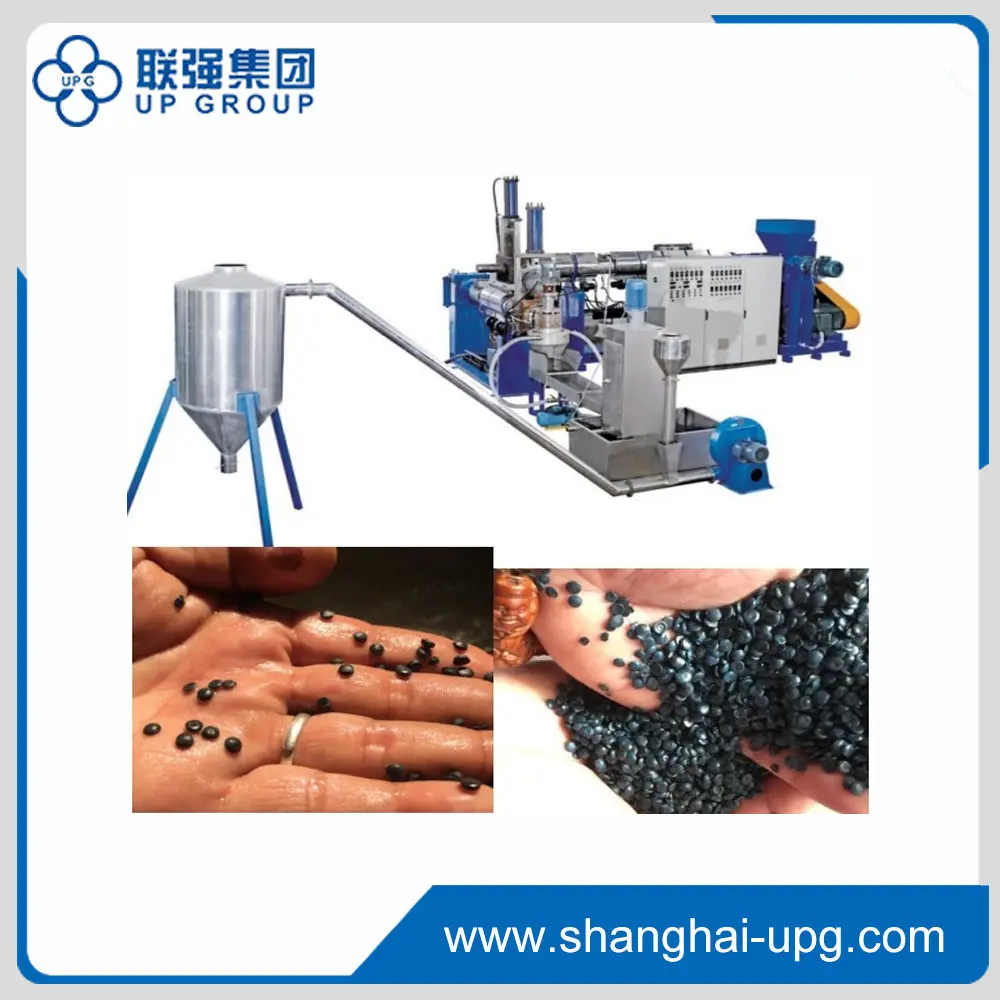
The Role of Automation in Plastic Container Machinery
Against the backdrop of technological advancements, automation has become an inaccessible part of plastic container making, with automated systems increasing productivity, reducing labor costs and improving product consistency. Many modern plastic container machines are equipped with the following advanced features:
- Robotic handling: Robots can load and unload molds automatically, increasing speed and reducing the risk of human error.
- Real-time monitoring: Sensors and software can monitor the production process in real time so that adjustments can be made immediately to maintain quality.
- Integration with other systems: Automated equipment can be integrated with inventory management and supply chain systems for seamless operations.
Environmental factors: As environmental awareness grows, manufacturers are increasingly focusing on sustainability, recycling materials and developing biodegradable plastics. Further development of machinery and equipment will make the production process more efficient, thus minimizing waste and energy consumption.
In summary, the production of plastic containers relies on a variety of specialized machinery, each of which is suited to a different production process. Injection molding, blow molding and thermoforming are the main methods used to manufacture these basic products. Automation and sustainability will play a key role in the evolution of plastic container manufacturing. For people looking to enter the plastic manufacturing industry or seeking to optimize production capacity, it is vital to understand the machinery and equipment involved in this process. People who are interested in how to make plastic containers or have a need to buy them, please contact us, we have advanced technology and experienced engineers.
Post time: Dec-30-2024